Density Meters / In-tank Density and Viscosity Meter
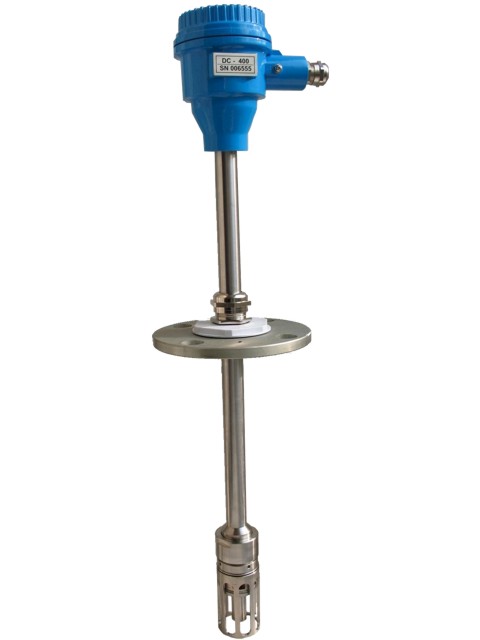
- Continuous, on line density and viscosity monitoring at process conditions
- Accurately measures density and viscosity of liquids with viscosity up to 2000cSt
- Rigorous factory calibration and testing of the transducer
- Can operate in pressurized tanks
- Immersion in the tanks up to 30 meters
- No moving parts, virtually maintenance-free system
- We also can tune system specification for your specific requirements
- Hazardous area approvals
- Insensitive to liquid level, mix or turbulence
- Large offer of standard product configurations and installation available
Use the proven vibrating element technique which is widely accepted as the most accurate method of continuous on line density measurement, LEMIS process engineers did new step ahead introducing unique proprietary design of resonant tube sensor allowing accurate measurement of liquid viscosity along with its density. An integral high accuracy Pt100 probe continuously monitors liquid temperature allowing temperature compensation and future calculation of reference viscosity, density, concentration or specific gravity. The technology proves high accuracy of measurement and long term calibration stability even in sever operation conditions. It is insensitive to plant vibration, high variation of temperatures, level, mix or turbulence.
The new sensor offers to plant engineers the ability to measure simultaneously and continuously both critical variables of the process liquid in one device saving cost of installation and maintenance. The DC42 series covers wide range of density, viscosity and temperature. Numerous installation options give large flexibility to fit various applications. The sensor can be directly inserted into the opening in a tank wall or can be submerged into a tank at desired level up to 30 meters. This technique can be employed in open or pressurized tanks and reactors. Large choice of process connection flanges is available. The meters have approvals for use in hazardous areas.
A choice of wetted parts materials : from stainless steel for general industrial use, Ni-SpanC for most demanding applications, and Hastelloy for applications where ultimate corrosion resistance is required. If you have specific requirements over the standard list, we can tune system specification for your specific needs.
Dynamic Viscosity Range |
0.2 to 2000 mPa·s (0.2 to 2000 cP) |
|
Dynamic Viscosity Accuracy |
±1% of span |
|
Viscosity Resolution |
0.1 mPa*s (0.1 cP) |
|
Dynamic Viscosity Repeatability |
±0.5% of span |
|
Density Range |
0 to 3 g/cm³ (0 to 3000kg/m³) |
|
Density Accuracy |
Up to ±0.00025 g/cm³ (up to ±0.25 kg/m³) |
|
Density Resolution |
±0.0001 g/cm³ (±0.1 kg/m³) |
|
Density Repeatability |
Up to ±0.0001 g/cm³ (up to ±0.1 kg/m³) |
|
Temperature Range |
-200°C to +200°C (-328°F to +392°F) |
|
Temperature Accuracy |
±0.1°C (±0.2°F) |
|
Pressure Range |
Up to 100 Bar |
|
Ambient temperature |
-40°C to +85°C (-40°F to +185°F) |
|
Viscosity compensation |
Automatic |
|
Temperature compensation |
Automatic |
- Petroleum products, fuels, lubricants, LPG, LNG
- Concentrations of acids or corrosive chemical
- Food, Dairy & Beverages
- Product identification and consistency
- Concentration and dilution measurement
- Monitoring of reaction end in reactors
- In-tank mixing and blending